Automation of production on elevators
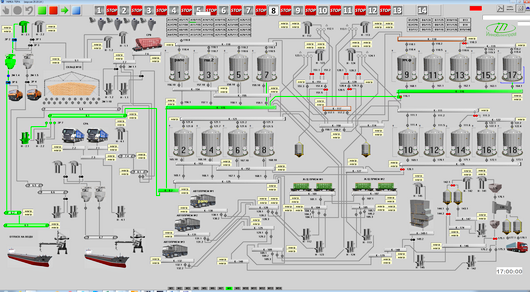
The system of remote automated control of the elevator of INNOVINNPROM LLC (RACS-E) is intended for the automation of the processes of storage, movement, loading / unloading, drying of grain products on elevators. The system provides automatic control of equipment operation, accounting for necessary technological delays, compliance with technological algorithms.
The use of RACS-E allows you to significantly increase the productivity of the elevator and reduce economic losses due to the elimination of staff errors when working with the equipment, reducing energy consumption as a result of automatic selection of the least energy-intensive routes for the movement of grain products and reducing technological delays to a minimum, reducing the system response time in the event of an emergency situations.
RACS-E does not require highly qualified staff and strict knowledge of the specifics of the operation of each unit of equipment. It is enough for the operator to indicate the starting and ending points of movement of grain and grain products. RACS-E will offer several optimal routes, starting with the least energy-intensive one. Therefore, the RACS-E operator can be a person with a secondary or secondary-special education, who has minimal knowledge of elevator technology and basic skills in working with a PC.
In the process of operation, RACS-E does not require the continuous presence of personnel behind the monitor screens. It is enough for the operator to choose the route of movement of grain products and give the command to start / stop it, RACS-E will perform other actions automatically. In the event of an emergency, an alarm will be sounded. In case of equipment failure, the system will offer a new route.
In addition, RACS-E carries out automatic control of the movement of grain crops, preventing their erroneous mixing.
RACS-E provides accounting of the operation of each unit of equipment.
A temperature measurement system can be integrated into RACS-E.
To support the operation of the implemented RACS-E, the INNOVINNPROM service support system has been implemented, which provides the possibility of prompt remote resolution of technological scheme modernization issues, updating all levels, overcoming emergency situations without the developer's representatives visiting the facility.
Structure of RACS-E
When building remote automated elevator control systems, the following basic principles, developed on the basis of many years of successful implementation experience, are taken into account:
- high system reliability;
- system modularity;
- repeatability during implementation;
- the shortest terms of implementation;
- ease of setup and maintenance.
Programmable logic controllers (PLCs) perform the functions of equipment management, control of its condition and processing of emergency situations.
PLC software uses typical algorithmic modules (functional blocks) for the main types of executive devices and typical control tasks. Therefore, when implementing an automation object, the programmer's task is reduced to the adaptation of the PLC software to the object's specific equipment by adjusting the existing functional blocks.
During the construction of RACS-E, the possibility of using up to 32 PLCs at the same time is provided. This architecture has a number of advantages compared to a classic single-processor system:
- higher reliability of the system due to the distribution of the structure (territorially by WP, functionally by loading / unloading, type of storage, etc.);
- there is practically no limit on the number of input / output channels;
- the cost of the system is lower due to the reduction of the cost of the PLC and the reduction of labor costs for its programming (as a rule, a non-functionally saturated, easy-to-program PLC with minimally sufficient technical parameters is used).
The safety equipment includes frequency drives, soft starters of electric motors, circuit breakers, automatic switches, magnetic starters, control and protection relays, fuses, control buttons and push-button stations, cam and packet switches, signal lamps, etc. to be installed both individually and in complete stations, panels and control panels for both separate machines and aggregates, as well as entire technological lines.
Typical connection and control schemes made in accordance with the requirements of the standards are used to connect the equipment.
Automated workplace "Route"
The automated workplace "Route" (APMO) is equipped on the basis of a modern high-performance personal computer. As software, the unique automated design system "Route" developed by INNOVINNPROM LLC (CAD "Route") is used, which is a powerful software product specialized for the construction of automated process control for technological processes (ACS TP) of elevators and granaries.
The main "highlight" of CAD "Route" is the high-quality error-free performance of the tasks of routing the movement of grain products. For example, on an elevator with 200 units of various equipment, more than a thousand routes can be implemented. At the same time, the operator needs only to indicate the beginning and end of the route to move the Cereal Product. Thanks to this, the operator can be personnel with an average level of education, because CAD "Route" will automatically suggest, include and control the most optimal route, taking into account the state of equipment, already working routes and moving crops, in order to avoid mixing them.
The task of choosing from hundreds of possible routes the optimal one in terms of the amount of equipment and power consumption is available to be solved by not every SCADA system, especially if the SCADA system is universal with a huge number of grain complexes unnecessary for automation, which nevertheless take away resources. Therefore, as a rule, RACS, which are made on the basis of such SCADA, practically do not implement the task of automatic routing and require a higher level of operator training, which is not always possible in rural areas. The operator is forced to choose the necessary route only from a limited list of regular routes, or to include the route manually - device by device, which inevitably leads to the occurrence of errors and, accordingly, the occurrence of production and economic losses related to the human factor. In addition, the implementation of RACS on these SCADA systems requires significantly more human resources and time for their implementation - at least the involvement of two high-class programmers for two months to work directly in the SCADA environment (project configuration and writing device software modules) and a programmer to work with the PLC . At the same time, the customer receives a software product that is closed to him and cannot be changed, with fewer features necessary for the grain complex, which requires highly qualified personnel to ensure its operation and maintenance.
In contrast to the above, CAD "Route" is an open software product available for quick editing and tested on dozens of elevators, which provides a full set of functions necessary for elevator management.
Composition of CAD "Route":
- "Elevator Management" software;
- "Editor of images and properties" software.
Both software products are software products that have been fully developed and tested by many years of practical experience at dozens of agro-industrial complex enterprises. Both software can simultaneously function on the same PC and allow making changes in the technological scheme of the elevator WITHOUT STOPPING the equipment BY ELEVATOR SPECIALISTS.
"Elevator Management" Software
"Elevator Management" software performs the following functions:
- ensuring the given logic of the functioning of the technological complex;
- automatic start and stop of technological equipment;
- selection and launch of the optimal technological route for moving grain from the list of possibilities in terms of the number of equipment and power consumption;
- blocking mechanisms and routes as a whole;
- simultaneous launch of several non-intersecting routes;
- combining several routes;
- division of routes;
- launch of complex component routes;;
- quick change of existing routes;
- control of the operation of technological equipment and keeping protocols of stops and emergency situations;
- display of equipment status, as well as phases of technological processes.
The software provides the possibility for the operator to enter the grain movement route, control the correctness of the route and automated start / stop of the route with the necessary blocks, information service for the operator on the operation of technological equipment and aspiration networks.
The program includes transport equipment on routes chosen by the operator. At the same time, the operator enters into the system the equipment of the beginning and end of the route, and, if necessary, intermediate equipment. The inclusion of mechanisms in the route is carried out in the opposite direction of the grain flow, and the shutdown is carried out in the accompanying direction. It is possible to supply grain to the route when the transport equipment is working.
Example of the "Elevator Management" software interface:
"Images and Properties Editor" Software
The "Images and Properties Editor" software can be supplied (under the terms of the contract with the Customer) together with the "Elevator Management" software. The software "Images and Properties Editor" is intended for creating and editing the general scheme of the elevator, editing device parameters.
The software "Images and Properties Editor" developed by INNOVINNPROM LLC is the only high-level, full-fledged automated design (CAD) system on the market for the development of elevator control systems.
The "Images and Properties Editor" software performs the functions of creating and editing the general scheme of the elevator and equipment parameters. The number and type of controllers, input / output modules, assignment of inputs / outputs is set from context windows of equipment management and can be changed by elevator personnel in accordance with access rights.
The main functions of the editor:
- creation of a technological scheme of the elevator;
- input of equipment properties;
- editing the general scheme of the elevator;
- editing equipment properties.
Creating and changing the technological scheme of the elevator is carried out by selecting equipment icons from the program library and assigning properties to it, creating connections between equipment. Performing these actions does not require the staff to know programming languages, only knowledge of elevator technology and basic functions of the editor.