Automation of leuco sapphire growth facilities
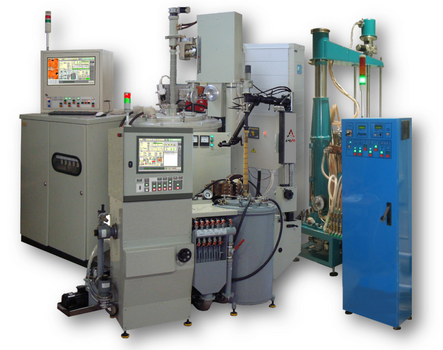
All stages of the technological process of growing single crystals are automated in the automated control systems (ACS) of the units for growing leuco sapphire by the Kiropulus method, with the exception of the crystal seeding stage, which requires a great deal of experience and practical skills of technologists. The transition from stage to stage is carried out automatically. The possibility of controlling the growth of the crystal both in terms of voltage and power has been implemented, and algorithms for controlling the growth of the crystal mass have been developed.
In order to prevent disruption of the crystal growth process and equipment destruction, multi-level system redundancy and comprehensive control of executive devices are provided.
In addition to the standard functions offered on the ACS market, the following innovations have been implemented:
- It is possible to connect an almost unlimited number of digital thermometers, which provides an opportunity to accurately control the temperature parameters of the heating unit and electric power equipment;
- The possibility of remote monitoring of the operation of the software at all levels, as well as its correction in accordance with the requirements of the technological process, remote software update, has been implemented;
- The possibility of "hot" transition to management from a backup PC has been implemented;
- A subsystem for remote seeding based on video camera data with the help of network equipment management software has been developed;
- A set of data sufficient to implement control of crystal growth by mass is provided.
ACS functions:
-
Measurement and registration of values of energy parameters of the heater;
-
Precise maintenance of voltage and power on the heater of the vacuum chamber;
-
Management of vacuum equipment, measurement and registration of vacuum values;
-
Single crystal extraction control and registration of displacement value;
-
Measurement and registration of single crystal weight values;
-
Measurement and registration of temperature and flow values in the circuits of the cooling system;
-
Automatic management of the process of growing single crystals;
-
Provision of blocking of emergency situations, signaling in case of their occurrence;
-
Formation of graphs and reports on the state of equipment and general information, such as the maximum and minimum value of parameters, dynamics of changes, system performance;
-
Demarcation of access rights to technological settings and protection of data from unauthorized access.
Constructive execution of the ACS CGF
It is carried out in a single industrial cabinet, which houses:
- Industrial panel computer;
- Industrial logic controller;
- Devices for input and output of discrete and analog control signals for CGF equipment;
- Meter and regulator of network parameters;
- Stepper motor drivers;
- Local manual control panel;
- Scheme of backup relay automation;
- Emergency alarm device.
Construction principles:
- Use of components from leading manufacturers of electronic equipment;
- Ensuring the maximum accuracy of measurement and maintenance of energy parameters of the heater;
- Multi-level control of CGF equipment parameters;
- Use of the minimum number of components;
- Galvanic decoupling of circuit components on power supply and interfaces;
- Using a modern PLC with a powerful processor, multi-level protection, a real-time counter, high-speed inputs and outputs;
- The availability of a relay automation scheme for blocking and alarming emergency situations;
- The possibility of emergency switching to control from a backup PC.
The process of growing leuco sapphire single crystals is long and, depending on the mass of the crystal, can last more than ten days. During the process, it is necessary to ensure precise observance of energy parameters, mass measurement, calculation and observance of the speed of crystal extraction, as well as adequate response of the System to emergency situations, such as disconnection and short circuit of the heater elements, temporary shutdown of the supply voltage, interruptions in the water supply of the cooling system. Therefore, in order to prevent the breakdown of the technological process of growing the crystal and the destruction of the thermal unit, a multi-level fault-tolerant architecture of the ACS CGF has been implemented, which includes the following levels:
1. Level measurement and control devices
This includes specialized controllers for measuring energy parameters (IP-3, IP-4), temperature (TKU-6M), and mass. These controllers ensure continuous and precise measurement and regulation according to the specified task.
2. The level of backup relay automation
It includes technological and emergency relays, automatic motor protection devices, time relays, buttons and is intended for non-automatic control of the system during tests, testing, calibration and keeping the system in working condition in the event of control errors and unforeseen situations.
3. Programmable logic controller (PLC) level
It directly includes a PLC and data input/output modules for control and management of vacuum equipment and is intended for conducting an automatic growth process.
4. Industrial computer (IC) level
It includes a IC, a monitor and network equipment and is intended for visualization of the progress of the technological process, data processing and archiving.
Software of ACS CGF
The SCADA system on the GNU/Linux OS platform is implemented as technological process management software.
The software has a multi-window interface and provides staff with complete information about the progress of the technological process and the state of the devices, convenient process management, demarcation of access rights, generates all the necessary reports and graphs, provides tools for viewing and analyzing data.
The software provides the ability to manage recipes of technological processes, including downloading recipes from the database, adjusting and saving the current ones.
PLC software functions:
- Introduction of analog signals of sensors and primary converters of technological parameters;
- Input of discrete signals of sensors-relays and state sensors of the main equipment;
- Normalization and filtering of analog signal values;
- Mathematical processing of normalized signal values;
- Control of values of calculated parameters and indications of technological emergency tolerances;
- PID regulation of technological parameters;
- Management of regulating and shut-off fittings;
- Generation of control inputs;
- Derivation of control influences on executive mechanisms;
- Control of the working out of control influences by executive mechanisms;
- Formation of data for dispatch control;
- Internal system data exchange and backup.
PC software functions:
- Visualization of technological process parameters;
- Assignment of technological process control parameters;
- Formation of diagnostic, warning and emergency messages;
- Logging and archiving information about the state of the equipment and the progress of the technological process;
- Generation and visualization of reporting forms;
- Formation of information for remote operators and users (including through the Internet);
- Temporary transition to management from a reserve workplace;
- Protection of data from unauthorized access at the level of user separation.
Implemented projects of the ACS CGF
ACS CGF PromCrystal-S2 passed industrial tests at the industrial facilities of GOE Crystal (Drohobych, Lviv region, Ukraine) where 18 crystals weighing 30 kg each were grown. The ACS CGF differed from its counterparts in modern software, which provides automation of all stages of growth, except for the stage of crystal seeding.
ACS CGF Delta-K was tested at the industrial facilities of Kvadrat-D LLC (Kyiv) and was exported to Shenzhen (PRC). New hardware and software solutions are applied in the ACS CGF to increase the level of automation of the growth process and maintenance processes. The IP-3M parameter meter was developed to control the energy parameters of CGF, and the TKU-6M universal technological controller was developed for multi-zone temperature control in the cooling system circuits.
ACS CGF Omega M300, Omega DM300 and Omega PG350 were developed in close cooperation with specialists of the Central Bureau of Mechanical Engineering "Donets" (Luhansk, Ukraine), and were tested at the factory facilities of Priroda LLC (Luhansk, Ukraine). CGF Omega M300 was delivered to the Scientific and Technological Complex "Institute of Single Crystals" of the National Academy of Sciences of Ukraine (Kharkiv, Ukraine). CGF Omega PG350 was exported to Guangzhou (PRC), CGF Omega DM300 was stolen to Russia during the occupation of part of the territory of Ukraine.
Omega DM300 and Omega PG350 CGFs are characterized by the use of a powerful power inverter as a source of heating the crucible, for monitoring the energy parameters of which the IP-4 parameter meter was developed.
!!! WARNING !!!
In connection with the events that took place in the east of Ukraine, the company lost a reliable, highly qualified partner for the production of grow plants - "Pryroda" LLC (Luhansk). But we have invaluable experience and knowledge of the technology of growing leuco sapphire single crystals and are ready for further cooperation in the industry. We are looking for new technological and financial partners.