Truck scales
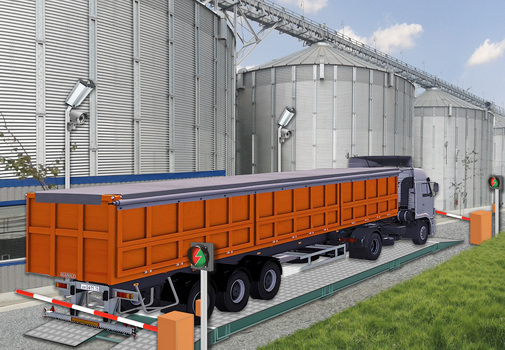
Every truck with grain arriving at the plant must pass a car weighing system. The weigher keeps track of the grain received at the enterprise. Weighing results are recorded in the weight log. Closely interacts with accounting software and grain or grain product accounting software, for example INNOVINNPROM "Sakura" System, and all information on accepted weight is automatically transferred to them. Provides the accounting department with all forms of reporting that have been done over a certain period of time. The silage board receives data on the weight of grain that has arrived at the enterprise.
For the release of products from the enterprise, it is necessary to have a consignment note and a certificate of product quality. A vehicle intended for loading finished products must pass the weighing scale. The quality of the shipped products is determined in the production and technological laboratory (PTL) On the basis of shipment data obtained from weighing, product quality obtained from PTL, a consignment note and a product quality certificate are drawn up.
Each weighing complex is designed individually on the basis of typical hardware and software solutions in accordance with the needs and requirements of the Customer. It is convenient when the scales are combined with an automobile sampler.
It is intended for registration of supplied raw materials and accounting of products shipped from the enterprise. Provides a significant reduction in the influence of the human factor on the results of weighing and accounting.
Features:
- Weighing of motor vehicles weighing from 0.5 tons to 60 tons with discreteness of reference - from 10 kg in automated mode;
- Accounting for the weight of accepted raw materials and released products;
- Issuance of goods and transport invoices upon shipment;
- Issuance of quality certificates upon shipment;
- Keeping weight logs and forming a summary of grain receipts by suppliers, owners, crops;
- Checking the correct installation of the car;
- Issuance of vehicle traffic control signals;
- Registration of the fact of the driver leaving the car;
- Integration of the video surveillance system.
Typical composition:
- Bar code scanners (RFID code);
- Information board;
- Barriers;
- Traffic lights;
- Position control sensors;
- Video cameras;
- Lighting lamps;
- Strain gauge sensors;
- System control cabinet with built-in controller and touch panel;
- APM of the weight master on the basis of a high-performance PC.
Working principle:
- A barcode (RFID code) is scanned (Assigned at the checkpoint, applied to the car door and entered into the GTN).
- If the bar code corresponds to what is expected, the number of the machine admitted to the scales is displayed on the information board, the green signal of the entrance traffic light and the red signal of the exit light are illuminated, and the entrance barrier opens.
- Positioning sensors monitor the correct installation of the car on the scales, and only after that the red signal of the entrance traffic light lights up and the barrier is closed.
- The weight is automatically fixed, stored in the system memory, and together with photographs of the moment of weighing, the weighing data is automatically transferred to the accounting system.
- The green signal of the exit traffic light lights up, the exit barrier opens.
Driver commands are shown on the information panel. Car movement is limited by barriers and regulated by traffic lights.
The complex monitors the facts of the driver's exit/landing from/into the car cabin.
Access to changing the operating modes and settings of the complex is carried out only in the presence of electronic keys with appropriate access rights. Also, the facts of opening the doors of the work cabinet are monitored and stored in the system memory in a log together with records of all without excluding the actions of the operator and the complex.
Production of truck scales
The company designs and manufactures new truck scales:
- With a bottom platform on 4 sensors;
- 2nd and 3rd platform;
- On 6 and 8 strain gauge sensors.
In addition, the existing mechanical scales will be modernized, namely:
- Re-equipment with strain gauge sensors;
- By increasing the size and carrying capacity of the platform;
- Modernization of weighing electronics;
- Delivery of the software of the automated workplace "Weighing".
Technical solutions
- The use of strain gauge sensons from the world's leading manufacturers;
- Typical platform lengths – 6, 9, 12, 18 m (designed individually);
- Versatility of installation of scales - on a reinforced concrete foundation in a pit of shallow depth or without a foundation on a concrete base, or on a reinforced concrete foundation in a ground layout.
Automated workplace "Autoweighing"
APM "Autoweighing" performs the functions of accounting for the weight of received and shipped grain that is shipped, grain waste and by-products of grain processing, accepted raw materials for the production of compound feed, finished products that are released - flour and compound feed, as well as cargo (grain, flour, grain waste , by-product) during inter-shop transfer:
Functions of the "Autoweighing" software workplace:
- Accounting for the weight of received grain;
- Printing of weighing results in the consignment note;
- Formation and printing of the act of deficiency;
- Formation of acceptance act;
- Accounting for the weight of goods, grain and grain waste being shipped;
- Accounting for the weight of the received raw materials on combined plants;
- Accounting for the weight of products, shipped flour;
- Formation of an act of commission weighing of flour trucks by container;
- Accounting for the weight of products that ship flour when loaded by flour trucks;
- Accounting for the weight of compound feed being shipped;
- Accounting for the weight of raw materials and finished products during intra-plant movement;
- Keeping weight logs;
- Formation of a list of documents on expenditure;
- Indication of the weight of the cargo on the weighing platform.
At the request of the Customer, equipment of any manufacturer can be installed, however, the company provides a controller of its own production SP-705, which is sufficient to perform most tasks of the weighing complex.