Automation of mills
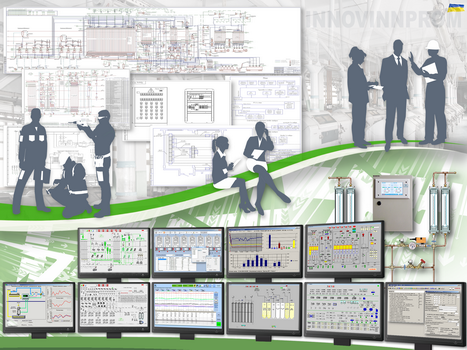
Automation of mills has been one of the company's priority areas for more than 25 years.
For more than 25 years in this direction, we have gained invaluable experience in the implementation of ACS TP at mills, including large two-section ones with a capacity of up to 600 tons per day. No engineering company of Ukraine can compare with "INNOVINNPROM" in terms of the number of implemented projects for full and partial automation of mills. The portfolio of implementations includes full automation of 20 mills in Ukraine, and the number of completed local tasks is measured in the hundreds.
The company has developed the only automated design system in Europe for the automation of grain processing enterprises, which allows you to automate an object of any complexity without error in the shortest possible time.
Control systems allow you to quickly and correctly start and stop the mill, change the modes of operation of the technological equipment, prevent and block the occurrence of emergency situations.
The composition of ACS TP includes a number of autonomous systems:
- A system of remote automated control of mill operation;
- The system of forming grain milling batches;
- System of moistening and dehumidification of grain before grinding;
- System of control and accounting of products at the entrance and exit of the mill;
- Control system of rolling machines;
- Current control system of powerful mechanisms and rolling machines;
- The system of accounting for engine hours worked by technological units;
- The system for issuing visual and voice notifications to the technological staff on the production floors of the mill.
ACS TP, with the help of automated operator workstations (APM), creates a convenient environment for visual monitoring of the operation of the mill equipment, automatically monitors deviations from the established modes, ensures the maintenance of an archive of all technological situations that arise.
The main functions of the ACS of the mill:
- Automated quick start and stop of the mill;
- Control of rotation of mechanism shafts, level of products in siloses;
- Current control of rolling machines, main mechanisms;
- Keeping schedules of mill outputs in real time;
- Prevention of emergency situations, automatic blocking, warning messages, automatic system actions;
- Continuous logging of all operator and system actions.
Implementation results
- Significant reduction of emergency situations, reduction of damage to electric motors;
- Prevention of piles of raw materials, breaks of conveyor belts;
- Optimization of the processes of formation of milling batches and preparation of grain for grinding by moistening;
- Improving the quality of flour, saving electricity, reducing the impact of the human factor.